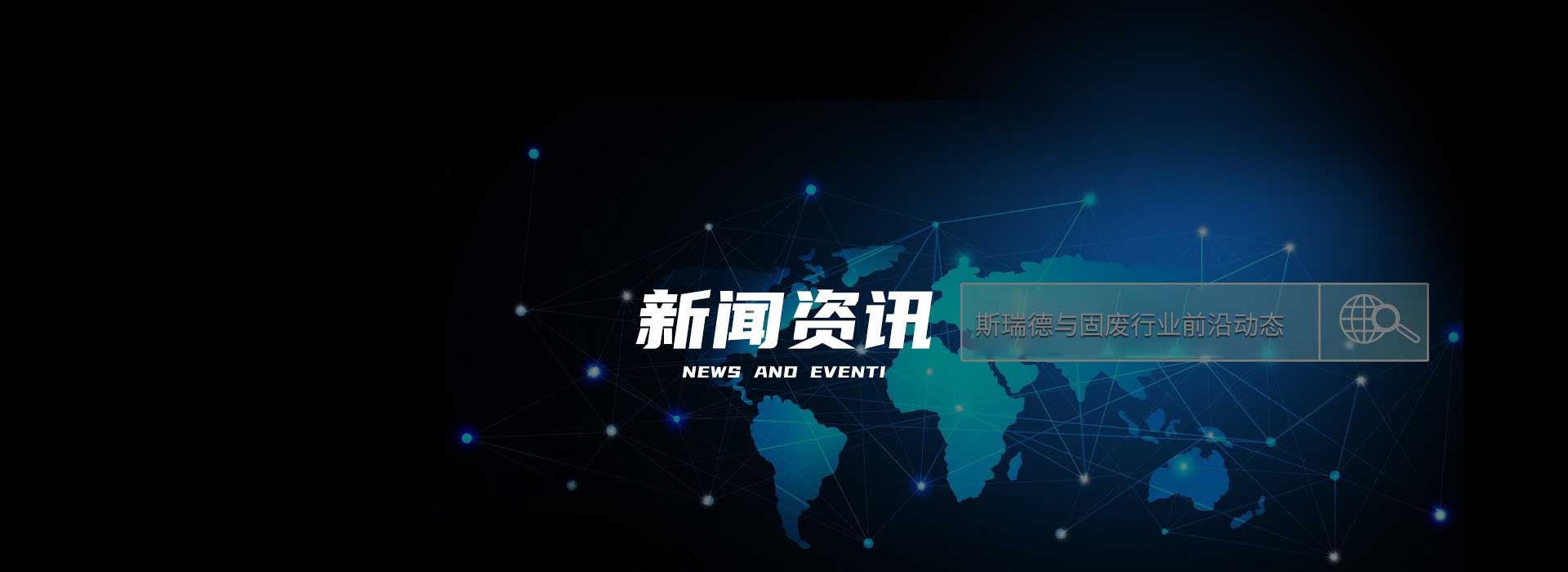
文章時間:2025年04月30日
在浙江紹興柯橋區,每年超 200 萬噸的紡織邊角料、殘次品堆積成山,曾因含染料、化纖難以處理,淪為填埋場的 “常客”。而如今,這些 “紡織垃圾” 正經歷一場神奇蛻變 —— 通過破碎、分選、磁選等工序,成為熱值達 5000 大卡 / 千克的 RDF替代燃料(垃圾衍生燃料),在水泥窯、熱電廠中替代燃煤,每噸 RDF 可減少 0.7 噸碳排放。這場從 “污染負擔” 到 “綠色能源” 的變革,正在改寫工業固廢處理的未來。
一、廢紡織固廢:藏在纖維里的 “雙碳密碼”
1. 固廢之困:產量激增與處理之痛
規模驚人:我國每年產生超 3000 萬噸廢紡織,僅廣東、浙江紡織集群年產生量就占全國 60%,其中化纖類占比達 70%,天然纖維(棉、麻)占 30%。傳統填埋不僅占用土地(1 噸廢紡織需 0.5 立方米填埋空間),化纖類降解需百年以上,天然纖維腐敗還會釋放甲烷(溫室效應是 CO?的 25 倍)。
環境代價:焚燒廢紡織雖能快速減容,但未經分選的廢紡織中的重金屬、化纖燃燒產生的二噁英等污染物,曾讓多地紡織園區被環保約談。而且,未經預處理直接焚燒,燃燒熱值不到2500大卡,熱值大打折扣,浪費了工業資源。
2. 政策東風:從 “末端治理” 到 “源頭利用”
《“十四五” 循環經濟發展規劃》明確提出,2025 年工業固廢綜合利用率需達 57%,廢紡織綜合利用被列為重點領域。與此同時,水泥、鋼鐵、造紙等行業納入碳交易市場,企業對低碳燃料的需求井噴式增長 ——RDF 替代燃料,正是破解 “減廢” 與 “減碳” 雙重目標的關鍵鑰匙。
二、技術解密:廢紡織如何煉成 “工業煤炭”?
根據斯瑞德廢紡織RDF替代燃料制備系統,可以看出實現 “纖維到燃料” 躍升的技術,一共分為四步:
1. 破碎:打破纖維壁壘
單軸/雙軸剪切破碎:采用斯瑞德破碎機,將大塊布料、線頭、紐扣等混合物破碎至 50mm 以下,刀片組可應對含金屬拉鏈、涂層布料等復雜原料,破碎效率比傳統單軸設備提升 30%。
2. 磁選 + 渦電流分選:通過磁選去除縫紉針、金屬扣,渦電流分離拉鏈中的鋁、銅等有色金屬,確保可燃物純度超 98%。
3. 干燥除雜風選:提純纖維熱值
斯瑞德風選機:利用氣流比重差異分離輕質雜質(如塑料袋碎片),靜電分選去除殘留的細微化纖粉塵,使可燃物含水率降至 8% 以下,熱值提升至 4500-6000 大卡/千克。
4. 重塑燃料形態
添加劑改性:按需添加石灰石(脫硫)、木質素(粘結劑),確保燃燒時 SO?、NOx 排放低于燃煤 50%,二噁英濃度控制在 0.1ng TEQ/Nm3 以下(國標 1ng)。
燃料配方:與生物質燃料按照一定比例進行混合,使其燃燒熱值得到進一步的提升。
三、斯瑞德廢紡織RDF替代燃料制備系統
斯瑞德針對廢紡織的原料特征,緊密結合替代燃料的入窯需求,提出了“碎更細、分更快、選更準”的固廢處理理念,以“模塊化、集成化、自動化”的設備相互組合,推出了更高效、更節能環保且兼容廢紡織等多種工業固廢垃圾的DWS替代燃料制備系統。
四、政策紅利與市場藍海:誰在搶占先機?
1. 政策 “組合拳” 激活市場
補貼支持:江蘇、廣東對 RDF 生產企業給予 80 元 / 噸處理補貼,對使用企業按替代燃煤量給予 50 元 / 噸獎勵。
碳交易賦能:根據測算,1 噸 RDF 可減少 0.65 噸碳排放,按當前碳價 80 元 / 噸計算,單噸燃料額外獲得 52 元收益,項目投資回收期可縮短至 3-5 年。
2. 萬億級市場待挖掘
傳統燃料替代:國內水泥窯年消耗煤炭超 5 億噸,若 RDF 替代率提升至 20%(歐洲平均 63%),年需求達 1 億噸,市場規模超 300 億元。
新興應用場景:造紙黑液焚燒爐、鋼鐵廠燒結機已開始試用 RDF,某河北鋼廠測試顯示,替代 10% 燃煤可降低燒結工序能耗 8%。
廢紡織的 “二次生命”,正在重塑工業未來。當剪刀剪下的布邊不再是垃圾,當堆積的殘次品化作窯爐里的火焰,我們看到的是 “無廢城市” 的真實模樣 —— 廢紡織等工業固廢垃圾不再是發展的負擔,而是循環經濟的 “綠色糧倉”。